Porosity in Welding: Identifying Common Issues and Implementing Finest Practices for Prevention
Porosity in welding is a prevalent concern that typically goes unnoticed till it causes substantial issues with the integrity of welds. In this discussion, we will certainly check out the key variables contributing to porosity development, analyze its harmful impacts on weld efficiency, and discuss the finest techniques that can be adopted to reduce porosity occurrence in welding procedures.
Typical Root Causes Of Porosity

One more regular wrongdoer behind porosity is the visibility of pollutants externally of the base steel, such as oil, grease, or corrosion. When these impurities are not efficiently eliminated before welding, they can vaporize and end up being trapped in the weld, causing flaws. Furthermore, using dirty or wet filler materials can present contaminations right into the weld, contributing to porosity problems. To mitigate these usual reasons of porosity, thorough cleansing of base steels, proper shielding gas option, and adherence to ideal welding parameters are important practices in attaining top notch, porosity-free welds.
Influence of Porosity on Weld High Quality

The existence of porosity in welding can significantly jeopardize the structural honesty and mechanical residential properties of welded joints. Porosity creates gaps within the weld steel, deteriorating its overall toughness and load-bearing capability.
Among the key consequences of porosity is a reduction in the weld's ductility and toughness. Welds with high porosity levels have a tendency to show reduced effect strength and reduced capability to flaw plastically prior to fracturing. This can be specifically worrying in applications where the welded components are subjected to vibrant or cyclic loading conditions. In addition, porosity can impede the weld's capability to effectively transmit forces, bring about early weld failure and possible safety hazards in important structures.
Finest Practices for Porosity Prevention
To boost the architectural integrity and quality of bonded joints, what particular measures can be implemented to decrease the incident of porosity during the welding procedure? Porosity prevention in welding is crucial to make certain the stability and strength of the last weld. One effective technique is appropriate cleaning of the base steel, removing any kind of pollutants such as corrosion, oil, paint, or wetness that could cause gas entrapment. Guaranteeing that the welding read this tools is in excellent condition, with tidy consumables and suitable gas circulation rates, can additionally considerably lower porosity. Furthermore, maintaining a steady arc and controlling the welding specifications, such as voltage, existing, and travel rate, aids produce a regular weld pool that lessens the risk of gas entrapment. Utilizing the proper welding technique for the certain product being welded, such as changing the welding angle and weapon position, can additionally prevent porosity. Routine examination of welds and immediate remediation of any kind of issues determined throughout the welding procedure are necessary methods to avoid porosity and generate top quality welds.
Value of Correct Welding Strategies
Implementing proper welding techniques is vital in ensuring the structural stability and quality of welded joints, building on the structure of reliable porosity avoidance procedures. Welding methods directly affect the overall strength and durability of the welded structure. One crucial facet of proper welding techniques is keeping the proper heat input. Too much warm can cause boosted porosity because of the entrapment of gases in the weld swimming pool. On the other hand, inadequate heat might lead to incomplete fusion, creating possible powerlessness in the joint. In addition, utilizing the suitable welding parameters, such as voltage, existing, and travel speed, is vital for attaining audio welds with minimal porosity.
Furthermore, the choice of welding procedure, whether it be MIG, TIG, or stick welding, ought to align with the specific requirements of the project to make certain ideal outcomes. Proper cleaning and preparation of the base metal, along with choosing the best filler product, are likewise vital components of skillful welding methods. By adhering to these finest techniques, welders can minimize the risk of porosity formation and create high-grade, structurally sound welds.
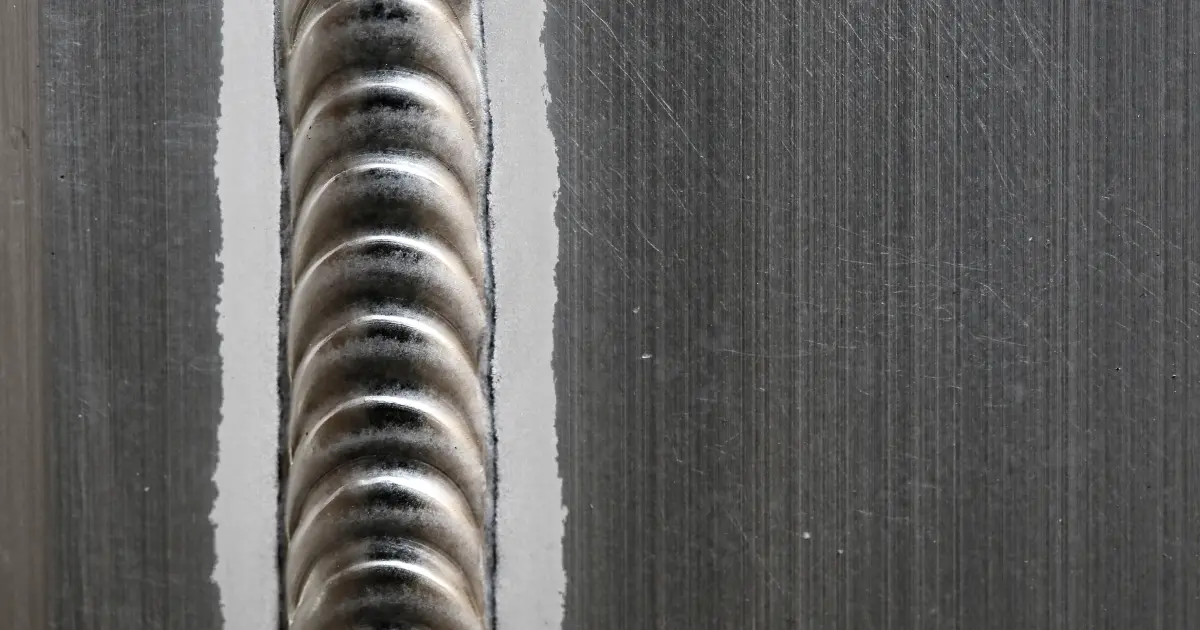
Checking and Top Quality Control Steps
Quality assurance actions play an essential function in validating the honesty and reliability of welded joints. Evaluating procedures are vital to find and avoid porosity in welding, making certain the toughness and resilience of the end product. Non-destructive screening approaches such as ultrasonic other screening, radiographic screening, and aesthetic inspection are commonly employed to identify possible problems like porosity. These strategies enable the analysis of weld quality without jeopardizing the honesty of the joint. What is Porosity.
Post-weld assessments, on Your Domain Name the other hand, analyze the last weld for any type of issues, consisting of porosity, and verify that it meets defined standards. Carrying out a detailed quality control strategy that includes complete screening procedures and inspections is critical to lowering porosity problems and ensuring the general top quality of welded joints.
Final Thought
In final thought, porosity in welding can be an usual concern that impacts the quality of welds. By determining the usual root causes of porosity and executing best techniques for avoidance, such as proper welding strategies and screening measures, welders can ensure high quality and trustworthy welds. It is essential to prioritize prevention methods to minimize the occurrence of porosity and maintain the integrity of welded frameworks.